
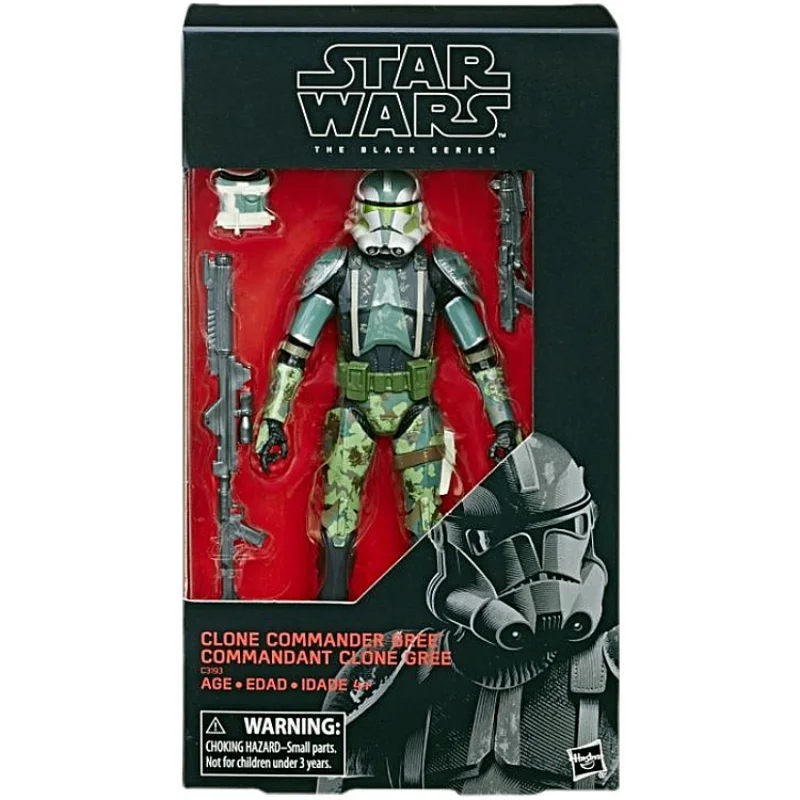
Since many players didn’t expect the chip shortage in 20, they likely had very limited stock available to weather the crisis. In normal times, the reduction of inventory is financially beneficial however, in the event of an unexpected shortage, the practice causes immediate disruption of the entire supply chain. Just-in-time manufacturing practices, which can minimize waste and increase efficiency by keeping on-hand inventory low, are widely leveraged in the auto supply chain. While the auto industry has had a good reputation for stable demand in the past, semiconductor manufacturers are now committed to more conventional, longer-term contracts from other fast-acting industries. With respect to binding purchase commitments on the order of a few weeks to a few months.
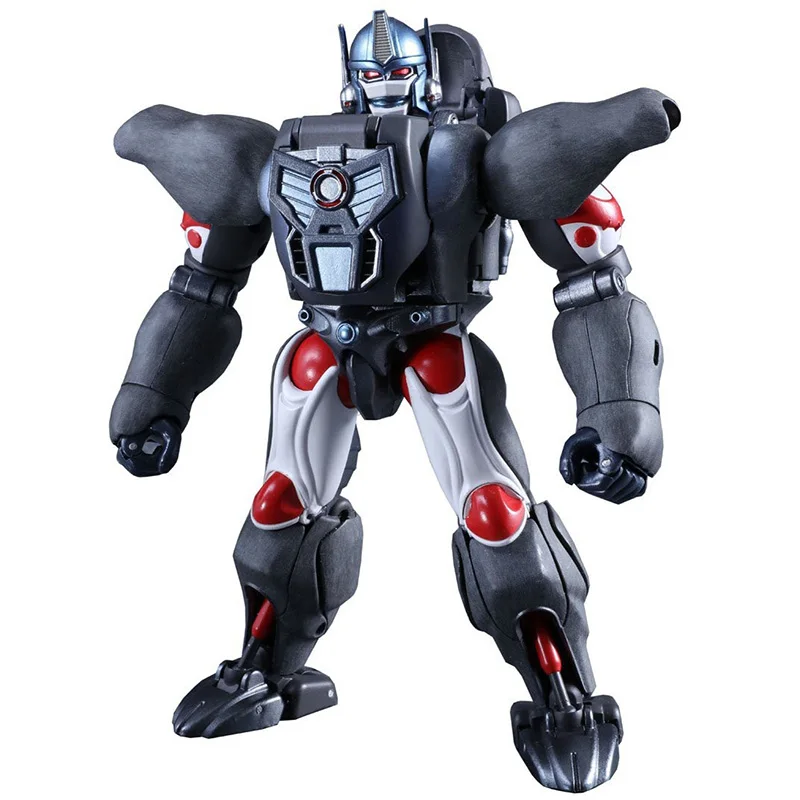
Amid an auto supply chain that is complex and often heavily outsourced, the chip-sourcing commitment cycle for the auto industry, however, tends to be shorter term-especially The typical contracts for sourcing parts in the auto industry differ significantly from other industries, which are more often governed by long-term binding agreements (so-called take-or-pay deals) and provide semiconductor suppliers with purchase orders that go well beyond six to 12 months. We estimate that such stockpiling caused a surge in semiconductor demand of 5 to 10 percent in the wireless space-the equivalent of one-third of auto-market chip sales. Please email us at: Geopolitical tensionsīecause of geopolitical tensions, some consumer-electronics makers have considerably increased their chip-inventory levels to get through a period of limited access to semiconductor manufacturing. If you would like information about this content we will be happy to work with you. We strive to provide individuals with disabilities equal access to our website. Because of that, when the auto sector’s demand recovered faster than anticipated in the second half of 2020, the semiconductor industry had already shifted production to meet demand for other applications. Over the same period, most other segments (with the exception of the industrial sector) experienced rapid expansion, resulting in an average increase from 5 to 9 percent in semiconductor sales beyond the forecasted growth. Our analysis of IHS Market data reveals that the actual demand for semiconductors in the auto industry in 2020 trailed a prepandemic estimate by around 15 percentage points (Exhibit 1). That meant that even as the auto industry drastically cut chip orders, other sectors faced an increased need. At the same time, driven by the shift to remote work and the associated greater need for connectivity, consumer demand significantly rose for personal computers, servers, and equipment for wired communications, all of which heavily depend on semiconductors. Moreover, while new-vehicle sales grew in the second half of the year, the highly ambiguous sales outlook at the time meant that automakers didn’t meaningfully increase their semiconductor orders. In the first half of 2020, the auto industry faced a substantial drop in demand. Instead, a confluence of events contributed to the situation the auto industry now faces.
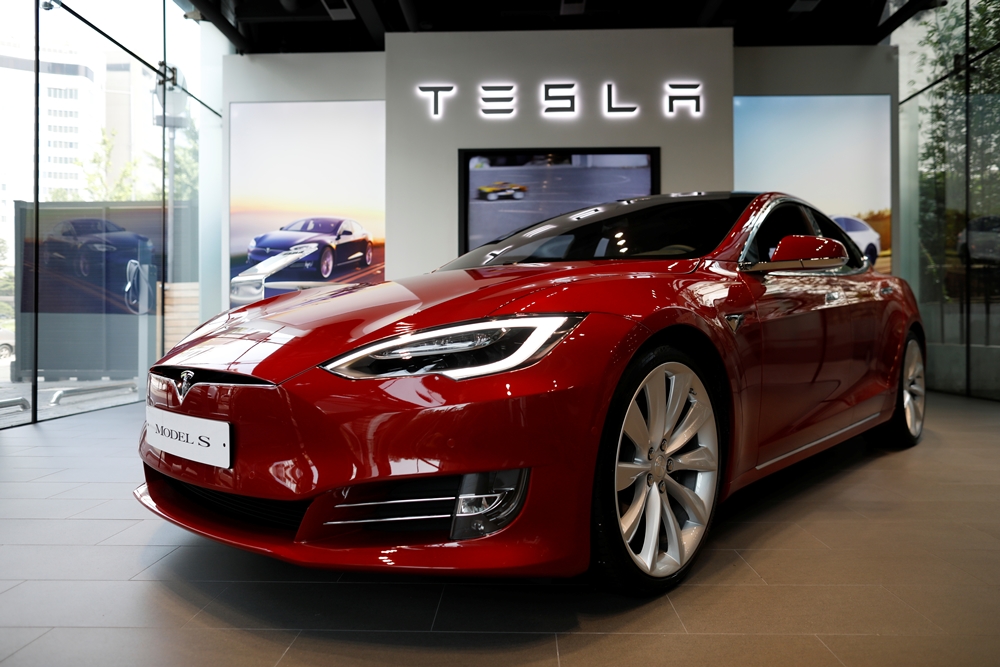
No single incident or disruption caused the semiconductor shortage. The effects of the semiconductor shortage have extended beyond the auto sector, with other industrial players struggling to secure chips. This article addresses both how the shortage happened and what remedies for it exist. Auto manufacturers and chipmakers alike will need to work together to tackle the imbalance in demand. Many automakers are now operating in crisis mode, and few expect a rapid resolution. That highlights the fragility of those supply chains, which largely rely on Asia as a hub of semiconductor manufacturing. The lack of demand for new cars shuttered auto factories and sent home millions of workers, while orders for semiconductors-used in myriad ways, including in fuel-pressure sensors, digital speedometers, and navigation displays-dropped off precipitously.
Price auto war series#
That challenge in the auto industry is the latest in a series of them that began in the early months of the COVID-19 pandemic, when auto sales plummeted as much as 80 percent in Europe, 70 percent in China, and nearly 50 percent in the United States.
